TECHNOLOGY技術・研究開発開発情報
水素技術で未来を拓く、時代の最前線となる金属セパレータ順送金型の開発
世界的な水素社会への動き
水素社会に向けた世界の取り組み
ウクライナ侵攻を契機に、エネルギー構造の変革が世界的に加速し、水素社会への移行に向けた動きも加速しています。
ドイツでは、水素導入目標が当初の2倍となる2030年までに10GWに引き上げられました。米国のインフレ抑制法(IRA)や各国における化石燃料との価格差縮小支援策なども推進されており、大規模水素製造プラントの建設計画も相次いで発表されています。 具体的には各国は以下のような取り組みを進めています。
- 支援策の充実
米国:インフレ抑制法(IRA)
各国:化石燃料との価格差縮小支援策 - 大規模水素製造プラントの建設
サウジアラビア:世界最大規模のプラント建設
豪州:大規模グリーン水素プロジェクト
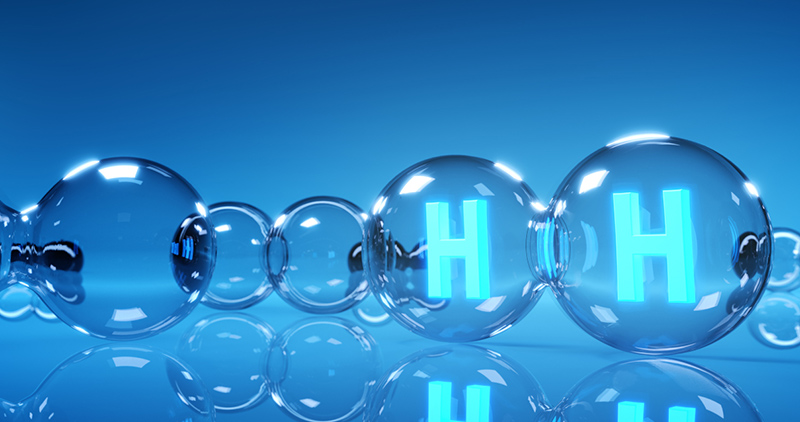
日本もこの流れを受け、2023年6月に水素基本戦略を6年ぶりに改定しました。
2040年までに水素等の導入目標を1,200万トンと新たに設定し、2030年までに国内外で水電解装置15GWの導入目標を掲げました。
日本は、水素技術において世界をリードする存在であり、今後も積極的に取り組んでいくことで、水素社会の実現に大きく貢献していくことが期待されます。
水素社会実装へ、大きく立ちはだかるコストへの壁
1. 燃料電池製造コスト
1つ目として燃料電池の製造コストが高いことです。
燃料電池には触媒や電極に高価な材料が使われており、それらが数百枚と積層されるため装置全体が高額なものになります。
2. 水素供給コスト
現状の水素供給コストは、一般的に1Nm3あたり100円~150円程度となり、計算するとガソリンより高くなってしまい社会実装は普及が思うように進みません。
順送金型による燃料電池金属セパレータのコスト低減
1. 高効率生産と高品質管理
燃料電池は、高効率かつ高品質な生産技術の開発が不可欠です。従来の生産方法では、これを実現するために膨大な設備投資とスペースが必要となります。
→今回開発した順送金型により、金属セパレータ製造の設備コスト圧縮や省スペース化が期待されます。
2. 材料ロスの低減
燃料電池の製造には、高価な材料を多く使用するため、材料ロスの低減が重要です。
→今回開発した順送金型は材料ロスを極力抑えるレイアウトにすることで材料コストの低減に期待されます。
3. 原料・プロセスの低コスト化
燃料電池のコスト低減には、原料や製造プロセスのコスト削減が不可欠です。セパレータの金属化による大幅なコスト低減と高生産性が期待されています。
→今回開発した順送金型は、金属セパレータをハイスピードで大量生産が可能となり、1枚当たりの製造コストを抑えることが期待されます。
4. 金型耐久性の向上によるコスト低減
金属セパレータは耐食性が高い材料を使用するため、加工難易度は増加します。コストを削減するためには金型の寿命向上も大きく求められます。
→今回開発した順送金型は、1μmオーダーの高精度金型部品の位置決め・クリアランス調整を行うことで金型の寿命向上が期待されます。
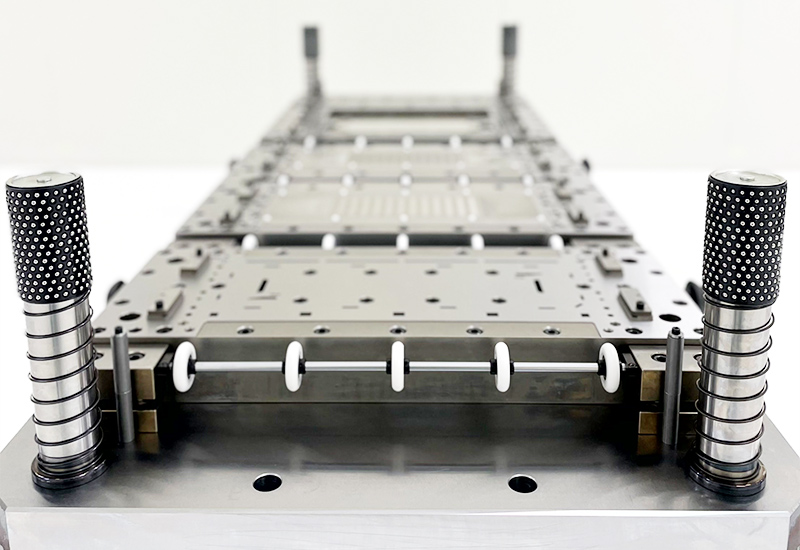

サイベックコーポレーションの新しい挑戦
弊社のCFP(Cold Forging Progressive)工法を活かし、金属セパレータ向け冷間鍛造順送金型の開発を行い、高効率生産による金属セパレータの低コスト化へチャレンジしております。
目標とする生産スピード
1分間の生産枚数
従来の生産ライン 6枚/分
目標の生産ライン 60枚/分
生産スピード10倍の向上を目指します。
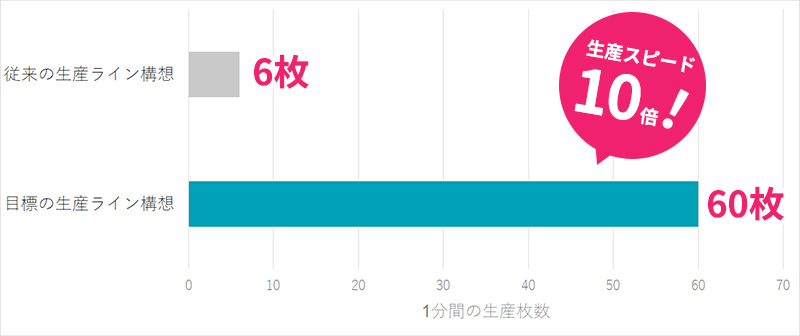
従来の生産ライン構想
ブランクを投入装置にセットし、ロボット等の搬送装置を用いて、各工程を搬送します。プレス機と搬送装置を連動させ各プレス機の冷間鍛造金型(単型)にて生産する方法です。

※製品形状等でプレス工程数は変動致します。
目指す生産ライン構想
材料はコイル材をダイレクトに投入し、金型内を送り装置で搬送します。使用する金型は冷間鍛造順送金型を使用。弊社のCFP(Cold Forging Progressive)工法を採用した生産方法です。

冷間鍛造順送金型のメリット
1. 設備投資額の削減
冷間鍛造順送金型になる事で、複数のプレス機、それを繋ぐ搬送装置が必要なくなり全体の設備投資額を圧縮できます。
2. 生産ラインの省スペース化
複数のプレス機、それを繋ぐ搬送装置が必要がなくなることにより、生産ラインがコンパクトになり、省スペース化を実現します。
3. 生産スピード向上
搬送装置のタイムロスがなくなり、プレス機の加工スピードに追従できる生産スピードを実現します。
今回開発中の冷間鍛造順送金型での製品サイズ
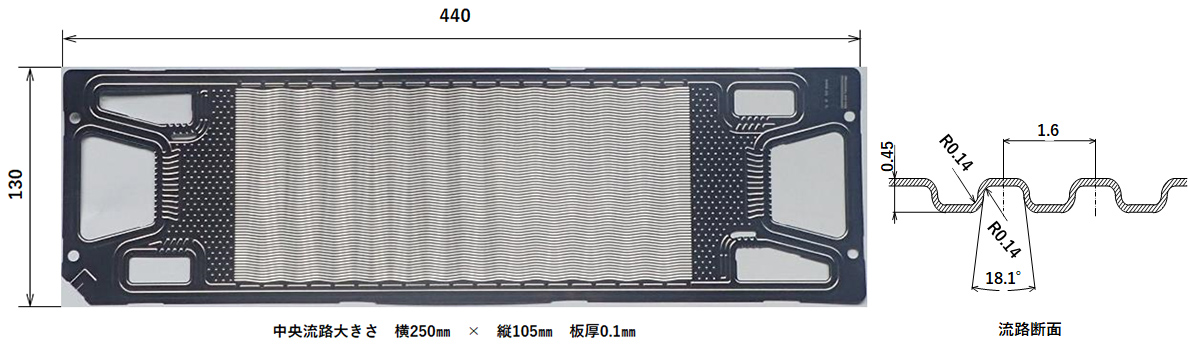
金属セパレータ順送金型動画
カーボンニュートラルに向けた燃料電池用金属セパレータ技術開発